ONE:Overview Regenerative incinerator (RTO) is a high-efficiency organic waste gas treatment equipment designed by the company on the basis of digesting and absorbing advanced technology from Europe and America, and adopting the method of "introduction + accumulation + improvement + innovation". The safety, stability and economy of this product have all reached European and American standards, making it an excellent choice to replace imported products.
TWO: Process flow
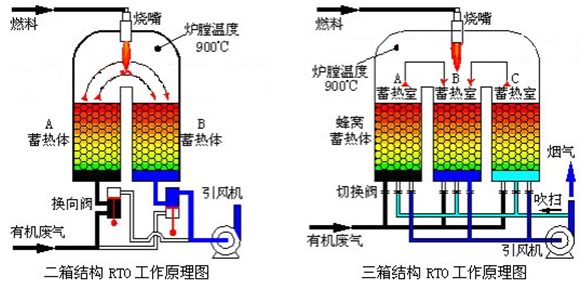
THREE:Process principle
The main structure of the two-bed RTO consists of a high temperature oxidation chamber, two ceramic regenerators and four switching valves. When the organic waste gas enters the heat storage body 1, the heat storage body 1 releases heat, the organic waste gas is heated to about 800°C and then burns in the high temperature oxidation chamber, and the high temperature clean gas after combustion passes through the heat storage body 2; the heat storage body 2 absorbs heat , the high-temperature gas is cooled by the regenerator 2 and then discharged through the switching valve. After a period of time, the valve is switched, the organic waste gas enters from the regenerator 2, the regenerator 2 releases heat to heat the exhaust gas, the exhaust gas passes through the regenerator 1 after being oxidized and burned, the regenerator 1 absorbs heat, and the high-temperature gas is cooled and then passes through the switch valve discharge. By switching periodically in this way, the organic waste gas can be continuously treated, and at the same time, no or a small amount of supplementary energy is needed to achieve the effect of energy saving.
In the case of high requirements for VOC emission concentration and emission rate, three or five regenerator beds can be designed, and each regenerator bed performs the cycle process of heat storage-heat release-cleaning in turn.
For organic gas with high concentration (less than 20% LEL), secondary waste heat recovery can be performed on the oxidized heat. The recovery method can be: heating heat transfer oil, steam, hot water, hot air, and hot air directly reused after filtering, etc. .

FOUR:Scope of application ● Medium and high concentration (less than 20% LEL), large air volume organic waste gas
● The exhaust gas contains a variety of organic components, or the organic components change frequently
● Not suitable for waste gas containing more silicone resin
Five: performance characteristics ● Higher VOC removal rate. The two-bed equipment is more than 95%, and the three-bed equipment is more than 99%.
● Ultra-low operating costs. When the VOC concentration reaches 450ppm, no additional fuel consumption is required. If the VOC concentration is higher, secondary waste heat recovery can be performed to greatly reduce the production cost.
● Thermal efficiency up to 95%
● No secondary pollution such as NOx is generated
● Processing air volume range of 5,000—200,000 cubic meters per hour
● Fully automatic control, easy to operate and easy to maintain
SIX. Selection parameter table
Model | RT0-100 | RT0-200 | RT0-300 | RT0-400 | RT0-500 |
Handling air volume m3/h | 8000-12000 | 18000-22000 | 27000-33000 | 36000-44000 | 45000-55000 |
Processing medium | Organic waste gas such as benzene, alcohols, alkanes, ethers, aldehydes, ketones, esters, etc. |
Gas concentration | 100~10000 mg/m3 |
Heat storage efficiency | 95% |
Purification efficiency | 95%~99% |
Operating temperature | 700~900℃ |
Burner | Heat supply | 174kw | 290kw | 580kw | 870kw | 1160kw |
Turndown ratio | Diesel fuel 5:1;Natural gas (or liquefied gas)30:1 |
Equipment resistance | ~3000Pa |
Note: For special specifications, it will be designed separately.